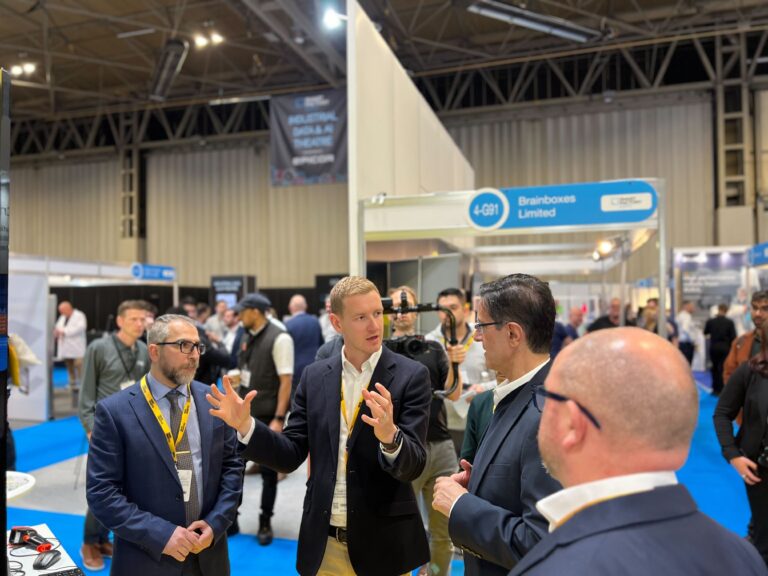
In the modern manufacturing landscape, where competitiveness and operational efficiency are paramount, data is the game-changer. As a manufacturer, you produce goods and a vast amount of data at every step of your operations. If exploited correctly, this data can illuminate inefficiencies, drive productivity, and even unlock new avenues for innovation. But where does one begin? What does the data journey look like?
Saleh Seyedzadeh, The Data Lab’s Principal Data Scientist for the Smart Manufacturing Data Hub, explores the components of unlocking potential and driving innovation in data in the manufacturing sector.
The power of data in manufacturing
Every machine, process, and employee interaction on the shop floor is a potential data point. When accumulated, these data points can tell a story—a story about how your machinery is operating, where there might be bottlenecks in production, or even how to better allocate resources during peak demand.
With energy costs fluctuating and the drive towards more sustainable operations becoming both an ethical and economic imperative, monitoring and optimising energy usage is a salient objective. Beyond that, data can help forecast demand, manage inventory, perform preventive maintenance, and enhance product quality.
Understanding data analytics and data science in manufacturing
Data analytics is the process of examining datasets to draw conclusions about the information they contain. In a manufacturing context, this involves:
- Descriptive analytics: Answering the question of what happened. This might involve assessing last month’s machine uptime or evaluating the efficiency of a recently introduced process.
- Predictive analytics: Determining what might happen in the future. For instance, analysing patterns to forecast machine failures or predict product demand.
- Prescriptive analytics: Offering solutions based on data. For example, suggesting changes to machine operations to optimise energy consumption.
Data science, on the other hand, deals with more complex problems. It applies scientific methods, algorithms, and systems to extract insights from structured and unstructured data. For example, it might involve machine learning to optimise processes or deep learning to improve product quality through image recognition.
The data science project process in manufacturing
- Problem definition: It is essential to identify the problem before diving into data. Is the aim to reduce machine downtime? Or is it to enhance product precision?
- Data collection: Gather data relevant to the problem. This might come from IoT devices, ERP systems, or even manual logs.
- Data cleaning: Raw data can be messy. It needs to be cleaned and preprocessed to ensure accuracy in analysis. This might involve removing outliers, filling missing values, or transforming variables.
- Exploratory data analysis (EDA): Before applying complex algorithms, it is beneficial to understand the data. EDA involves visualising data, understanding patterns, and identifying correlations.
- Model development: Using algorithms to build a predictive or prescriptive model. In manufacturing, this could involve creating a model to predict when a machine might fail.
- Validation and testing: Before deploying, the model’s accuracy and reliability are tested. This ensures that it works as intended in real-world conditions.
- Deployment: Once validated, the model is integrated into the manufacturing process. This might involve setting up real-time alerts for machine maintenance or an automated system to adjust production parameters based on predictive insights.
- Dashboarding: This involves presenting data in an intuitive and actionable way. Dashboards and visual representations can quickly convey the health of operations, KPIs, and areas that need attention.
- Feedback and iteration: Data science is an ongoing process. As new data emerges and conditions change, models might need adjustment. Continuous monitoring and feedback loops ensure the solutions remain relevant and practical.
Leveraging data analytics and data science in key manufacturing domains
Let’s explore the potential applications and benefits in performance management, condition monitoring, compliance management, process control, and quality control.
Performance management
Performance management in manufacturing typically revolves around evaluating, monitoring, and optimising operations. Data analytics can:
- Provide real-time insights: Using data analytics, manufacturers can gain real-time visibility into machine performance, operator efficiency, and production bottlenecks. This allows for swift decision-making and operational adjustments.
- Enhance productivity: Through predictive analytics, potential downtimes can be anticipated, and preventive measures can be taken. This keeps production lines running smoothly, enhancing overall productivity.
Condition monitoring
The health and operational status of equipment are paramount in manufacturing:
- Predictive maintenance: Data science, especially machine learning, can analyse historical and real-time machine data to predict when equipment might fail. This allows manufacturers to switch from a reactive maintenance approach to a proactive one.
- Extend equipment life: By understanding the equipment’s exact condition and stress factors, manufacturers can implement measures to extend machinery life, reducing capital expenditure in the long run.
Compliance management
Manufacturers often grapple with a myriad of regulatory and compliance requirements:
- Automated compliance reporting: Data analytics tools can automate the compliance reporting process, ensuring that reports are timely, accurate, and meet regulatory standards.
- Risk assessment: By analysing production data, manufacturers can proactively identify areas that might fall short of compliance standards, allowing them to address potential issues before they become critical.
Process control
Ensuring consistent and optimised processes is at the heart of manufacturing:
- Optimise resource allocation: Data analytics can provide insights into which processes are resource-intensive, enabling manufacturers to optimise resource allocation and reduce waste.
- Enhance process efficiency: Machine learning models can analyse production data to identify process inefficiencies. Once recognised, these inefficiencies can be addressed, leading to streamlined operations and reduced production costs.
Quality control
The quality of the final product is a direct reflection of a manufacturer’s commitment to excellence:
- Automated defect detection: Using advanced image recognition powered by deep learning, manufacturers can automate defect detection, ensuring that only products meeting the highest standards reach the market.
- Root cause analysis: If quality issues do arise, data analytics can help in conducting a root cause analysis, pinpointing the exact stage or component responsible. This allows for targeted corrective actions and continuous quality improvement.
Success stories: Real-world applications
To showcase the transformative power of data in manufacturing, let’s briefly delve into some case studies:
- GE Spares: Adopted low-cost IoT-based sensor technology to monitor and optimise energy consumption in their fabrication operations. The insights from the data allowed them to establish machine utilisation benchmarks and adjust operations to save on energy costs.
- Axon Power & Control: Transitioned from manual data input to a streamlined, automated system, tapping into comprehensive historical data. Through rigorous analysis, they refined inventory management, ensuring optimal stock levels and efficient resource allocation.
- Ryobi Aluminium Casting: Merged submeter data with production outputs, gaining holistic insights about their energy consumption profile. This data-driven approach provided a strong business case for further investment in energy platforms and drove their digital journey forward.
Conclusion
Data is not just numbers and charts; it’s the lifeblood of modern manufacturing. Think of it as the hidden script that holds the secrets to efficiency, productivity, and innovation.
If you’re in manufacturing and haven’t yet tapped into the power of your data, you’re not just missing out on charts or graphs; you’re potentially overlooking transformative insights that could redefine the trajectory of your business.
It’s a compass, pointing out both challenges to overcome and opportunities to seize. In this rapidly evolving industry, being equipped with this compass might be the critical difference between leading the change or playing catch-up.
So, if you’re a manufacturer yet to set out on your data journey, there’s no better moment than now. With platforms like the Smart Manufacturing Data Hub and the benefits demonstrated by pioneers like GE Spares, Axon, and Ryobi, it is evident that data-driven manufacturing is not just the future but the present. Embrace it, and watch your operations transform.